Part
of restoration work involves replacing damaged gears and pinions.
Gears are the large diameter brass parts with many teeth. Pinions
are smaller in diameter and as a rule have no more than 12 leaves and
are constructed of steel. The damage to this gear is
obvious. The new gear must be of the same diameter and have the
same number of teeth. If the restorer is lucky, one of the
existing cutters will be the right size. However, there are many
times when a cutter must be made.
I
was lucky on this wheel. A .35 module commercial cutter was a very
nice fit between two undamaged teeth.
Turning
a wheel blank to slightly oversize for the new gear.
Fitting
the turned wheel blank to an arbor that will support the wheel teeth
against the forces generated during the cutting process.
Here
the wheel is mounted on its cutting arbor which is then mounted in a
lathe headstock. The lathe headstock is mounted on a WW lathe bed
machined to fit the table of a small horizontal mill. These mills
are far more rigid than any wheel cutting engine ever sold for cutting
horological gears. Plus, since they were made by the thousands for
machine shops during the 40s and 50s and are now obsolete, they can be
found at very reasonable prices. I then decided to machine an
extra lathe bed so that I could use a WW lathe as my dividing head.
Since
the lathe bed ensures the "truth" of the centers of my
tailstock and headstock (they are an original paired set), I can use a
male center in the tailstock to center my cutter. I can also use
the tailstock to support the sttel stock when I am cutting pinions.
This
is what the setup looks like. You can see the set of dividing plates
to the left of the cutting set up. The correct dividing plate is
mounted on the rear of the headstock. Dividing plates are discs
with accurately located notches evenly spaced around their
circumference. Different numbered plates allow you to cut gears
with different numbers of teeth. Most sets go include plates
between 50 and 100 divisions.
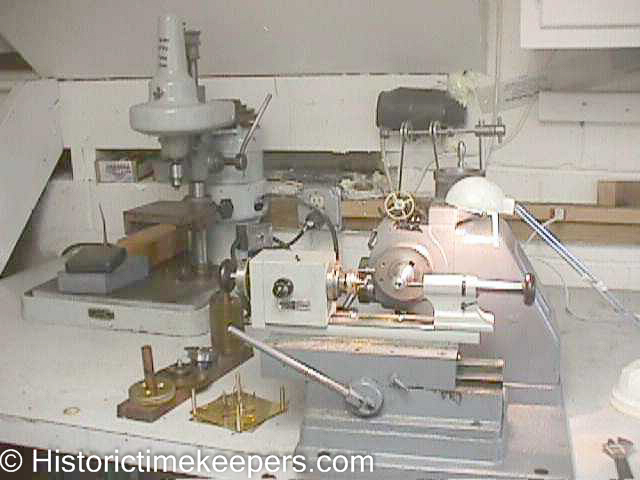
Cutting
the teeth.
The
teeth have now been cut.
Another
view of the teeth being formed (the new teeth are to the right of the
cutter).
Checking
the depthing of the new wheel with its mated pinion (mounted in the
frames of the brass depthing tool) against the original holes in
the clock plates.
|