It was easy to service a timepiece
when parts were available off the shelf. However, that is becoming
increasingly rare. Mainsprings for vintage pieces are no longer
made, and I cannot even get another run of mainsprings I had custom made
in Switzerland for the Waltham CDIA and 37500 Elgin/Hamilton Aircraft
clocks. Many workers routinely reuse the 70 year old spring they
find in the clock. Worse, they may offer to install new/old stock
mainsprings. These are blue carbon steel springs. No one has
made these for 60 years and they can either "set" or have
started to corrode. They can break catastrophically damaging the
instrument. A new blue steel spring is worse than the used one
because while the used one is fatigued, the 60 year old unused spring
often shatters at full power within a year or so with devastating
results.
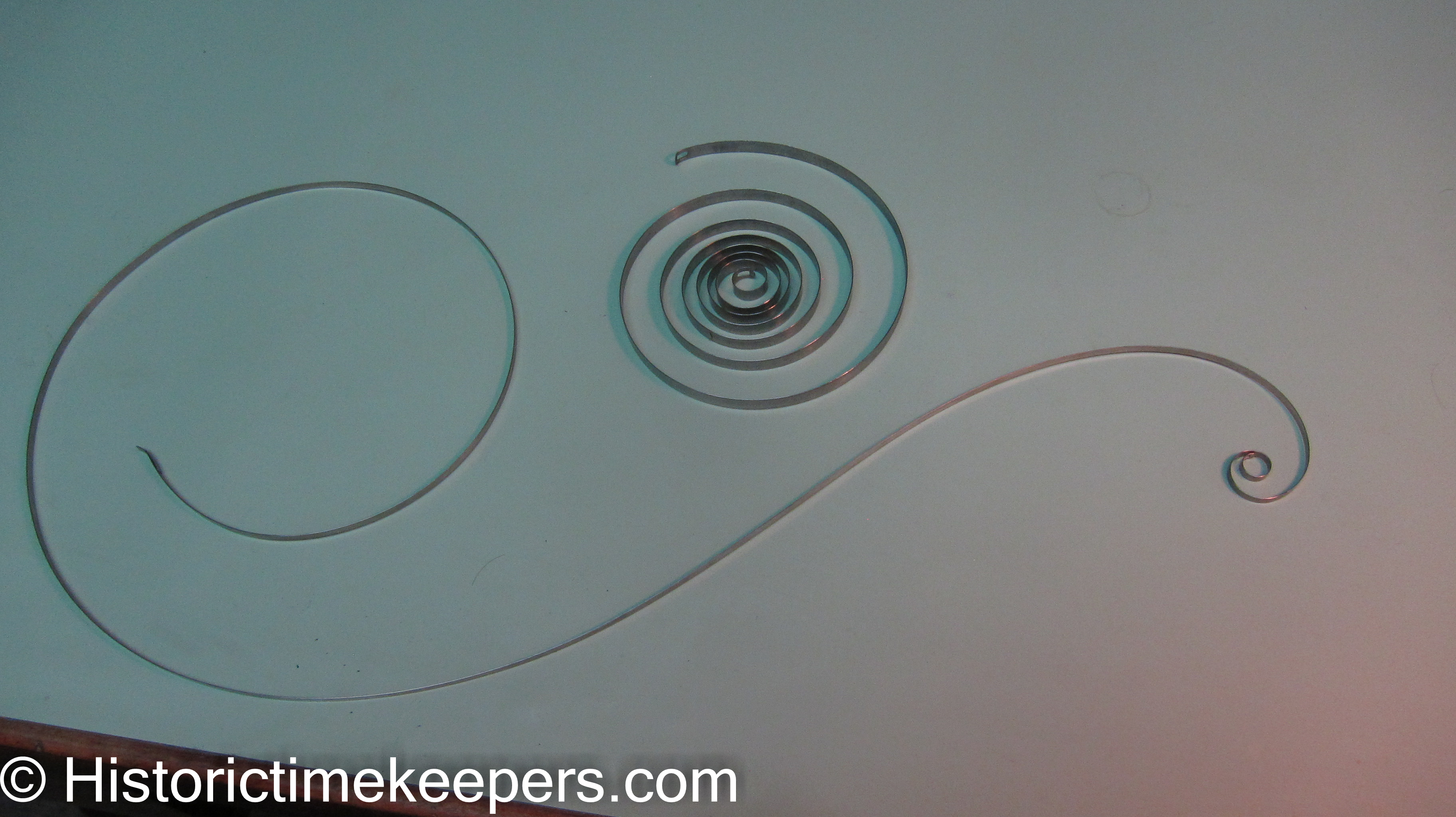
New Stainless Steel and set blue
steel springs (37500)
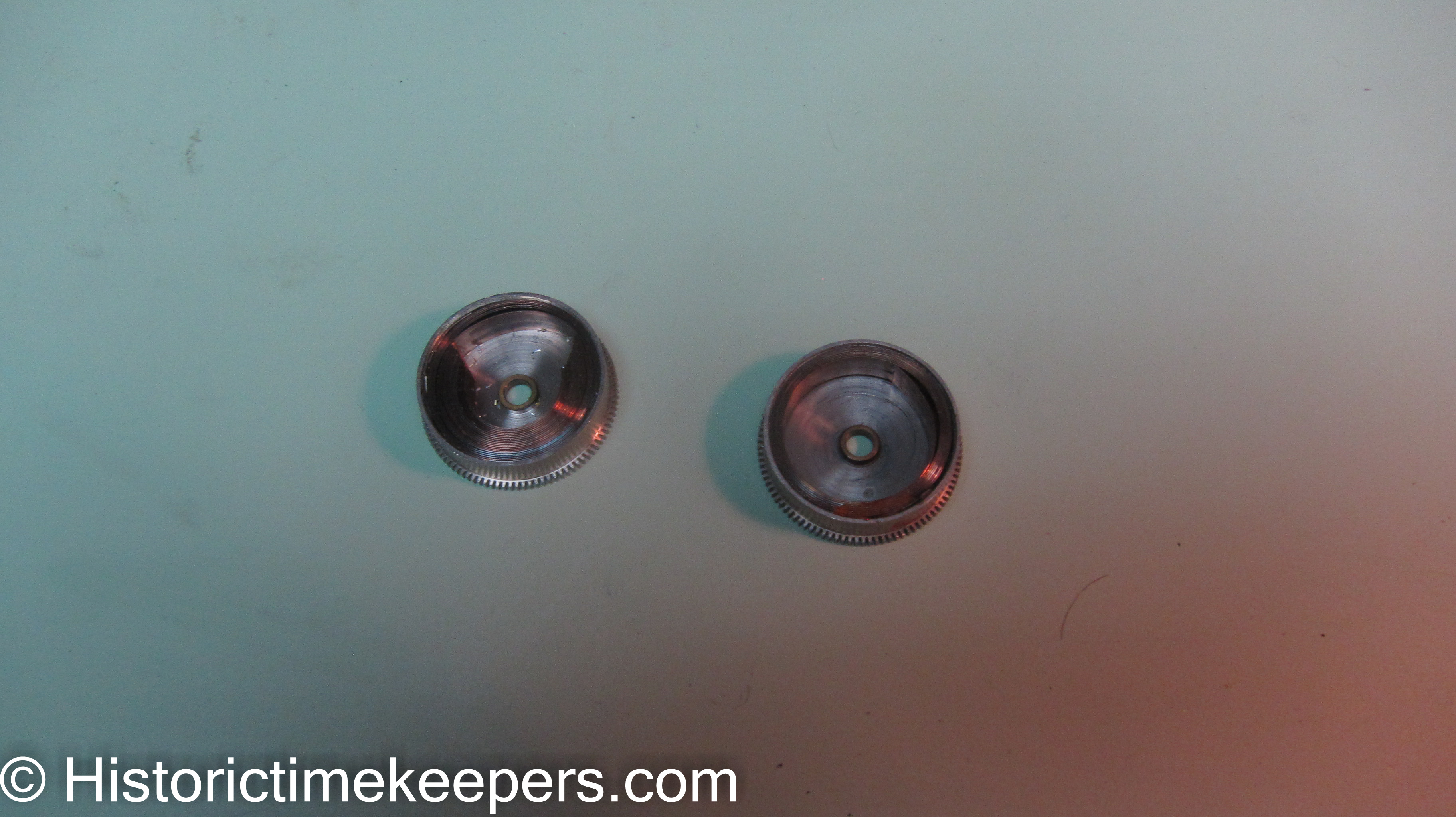
Shattered and rusted 37500 blue
steel springs
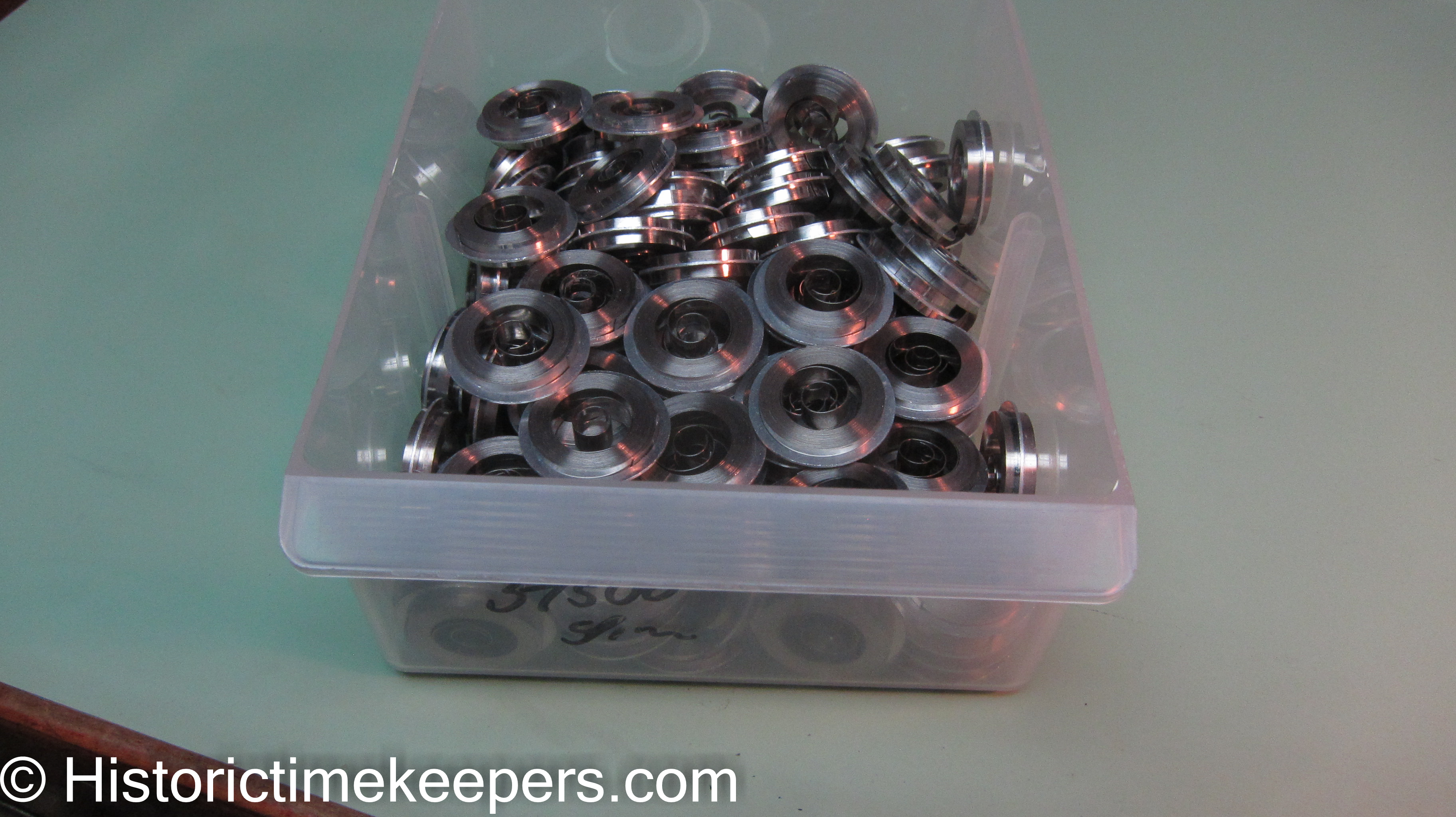
Custom Swiss made SS
("unbreakable" ) 37500 Springs
Balance staffs are another issue.
Years ago I started buying up aircraft clock balance staffs from the
material houses because I had learned that vintage balance staffs were
no longer being made (same with jewels). I have staffs for
everything from the 37500 and CDIA to the Jaeger LeCoultre and Mathy
Tissot Type 12.
When a worker does not have the part,
he will frequently hope to "get by" by using the broken part,
or if not a watchmaker, he may not even recognize it. I recently
had an MSR Z8 (sold under various names such Thommen, Longines, etc.)
that was sold to a customer and even had a recent FAA cert on it by the
company that sold it. It did not keep time. Reason was the
balance staff upper pivot was worn to a nub from lack of lubrication.
I quoted the job. Looked at my stock, no staff. Called a
couple material houses, no stock. So, I made the staff and held to
my quote even though I charge twice as much for a custom staff as for a
replacement. But I missed the quote. So it goes.

MSR Z8 with custom staff. Aesthetics are
meaningless if the piece is not functional
Bear in mind that the MSR Z8 is a
"modern" movement, manufactured into the 1990s. But
replacement parts for mechanical aircraft clocks are obsolete and many
"breakable" parts are simply unavailable.
Cracked jewels that are allowed to
remain are a major source of lubrication problems. The crack draws
the oil away via capillary action. These must be replaced or the
work refused. Worse, a damaged jewel can cut the pivot itself
impacting timekeeping and even cutting straight through with the expected
results. Unfortunately, someone not trained in watch service will
not know enough to look or may not even possess a microscope to aid in
inspection. And if he did not stock up on jewels or purchase the
equipment for their replacement ......
Extreme example of cracked plate set jewel requiring traditional
replacement technique shown here
Some of the friction jewel inventory
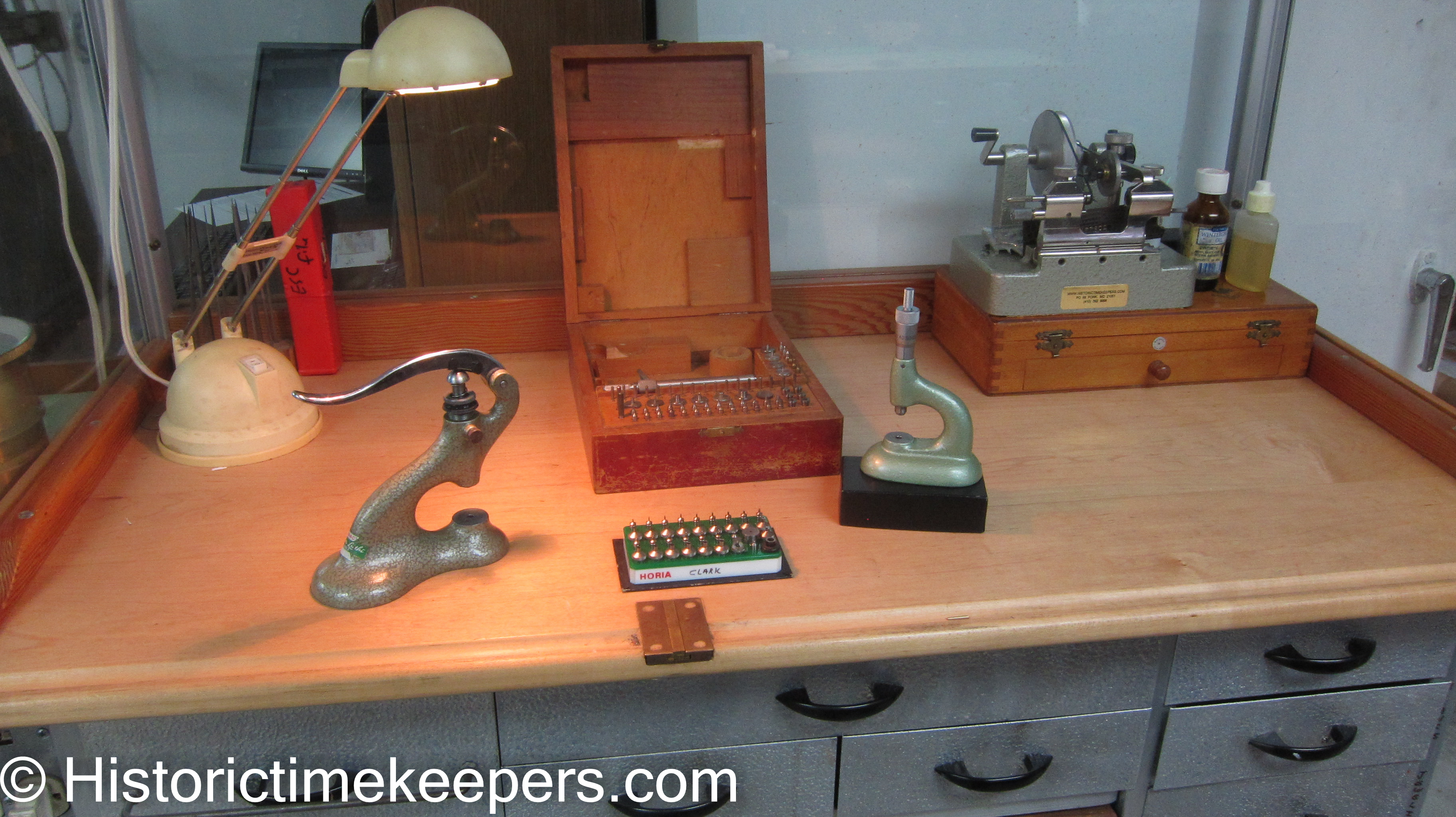
Equipment used for precise replacement of friction jewels
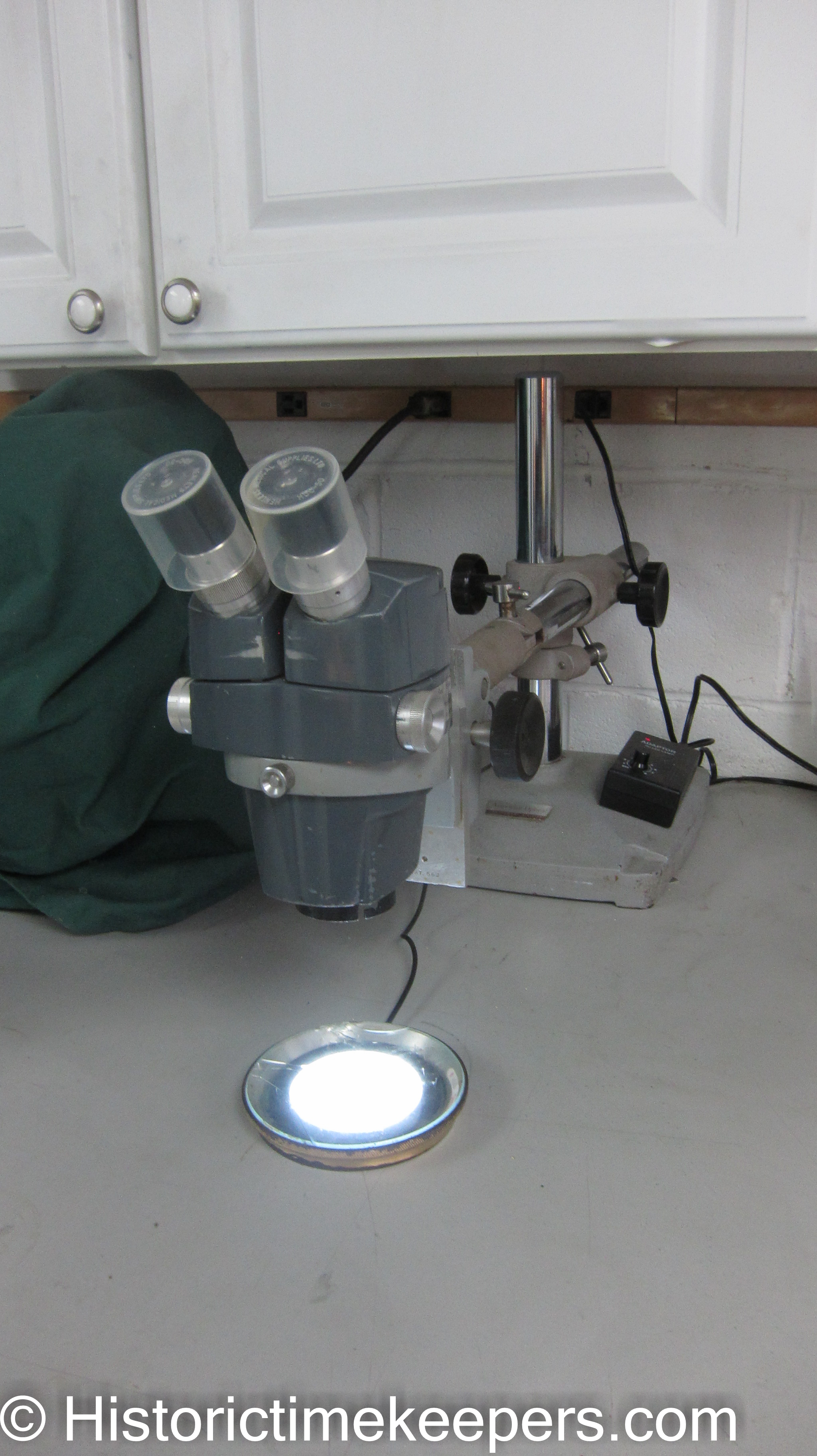
Good high powered optics for inspection
To learn more about the usefulness of
microscopes, visit our Microscopes in
Watchmaking page.
Then comes the problem of an important
timepiece for which parts are not available. I often encounter
Jaeger LeCoultre aircraft clocks with broken winding stems or winding
wheels. These are broken because the vintage Swiss clocks "wind
backwards" and have no clutch. I have seen pliers marks on the
knob from attempts to wind them when the user was unaware of this fact.
Verifying manufactured Jaeger stem against sample
Since these parts are not available they
have to be made. While lathe work is not rocket science, it does
require skill and experience to measure, plan and execute the work;
including knowing how to make the proper gear cutter to mill the teeth of
gears and pinions when that cutter is not already part of the shop's
library.
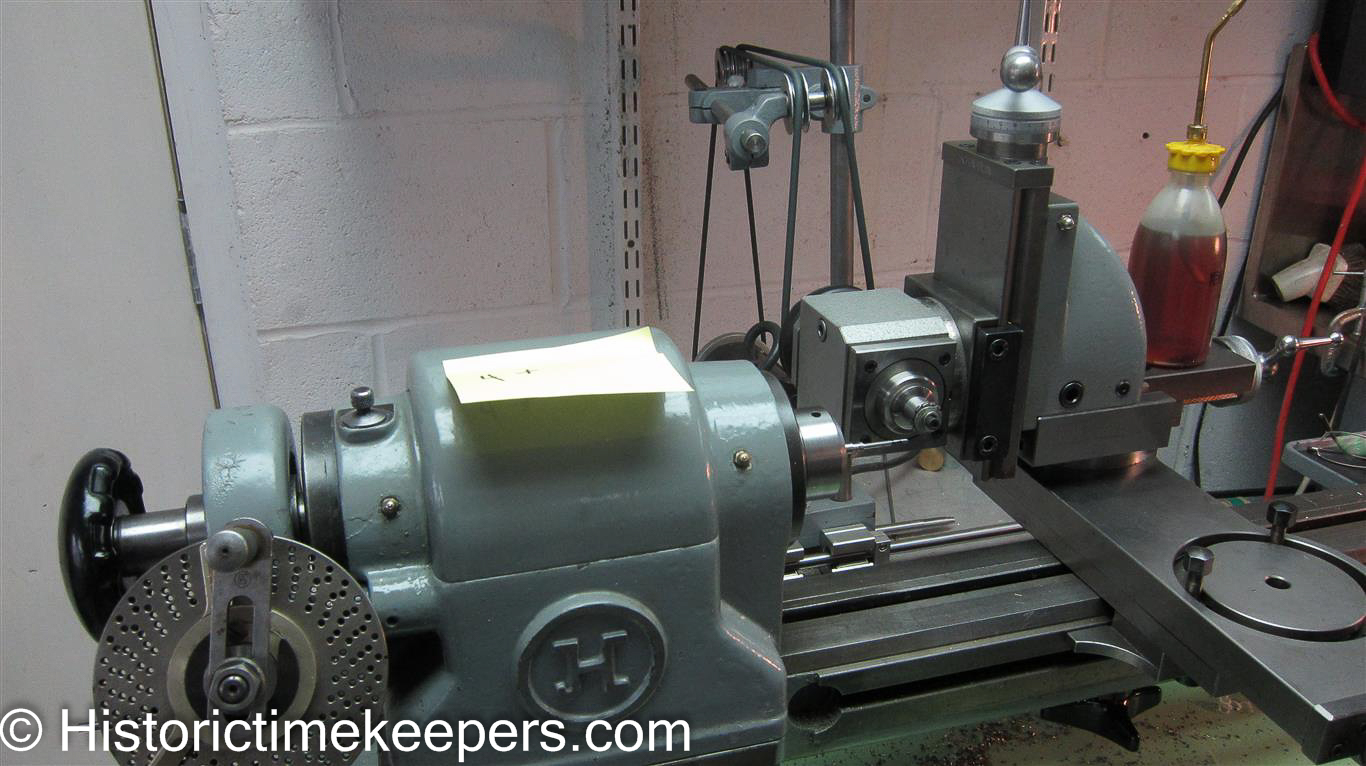 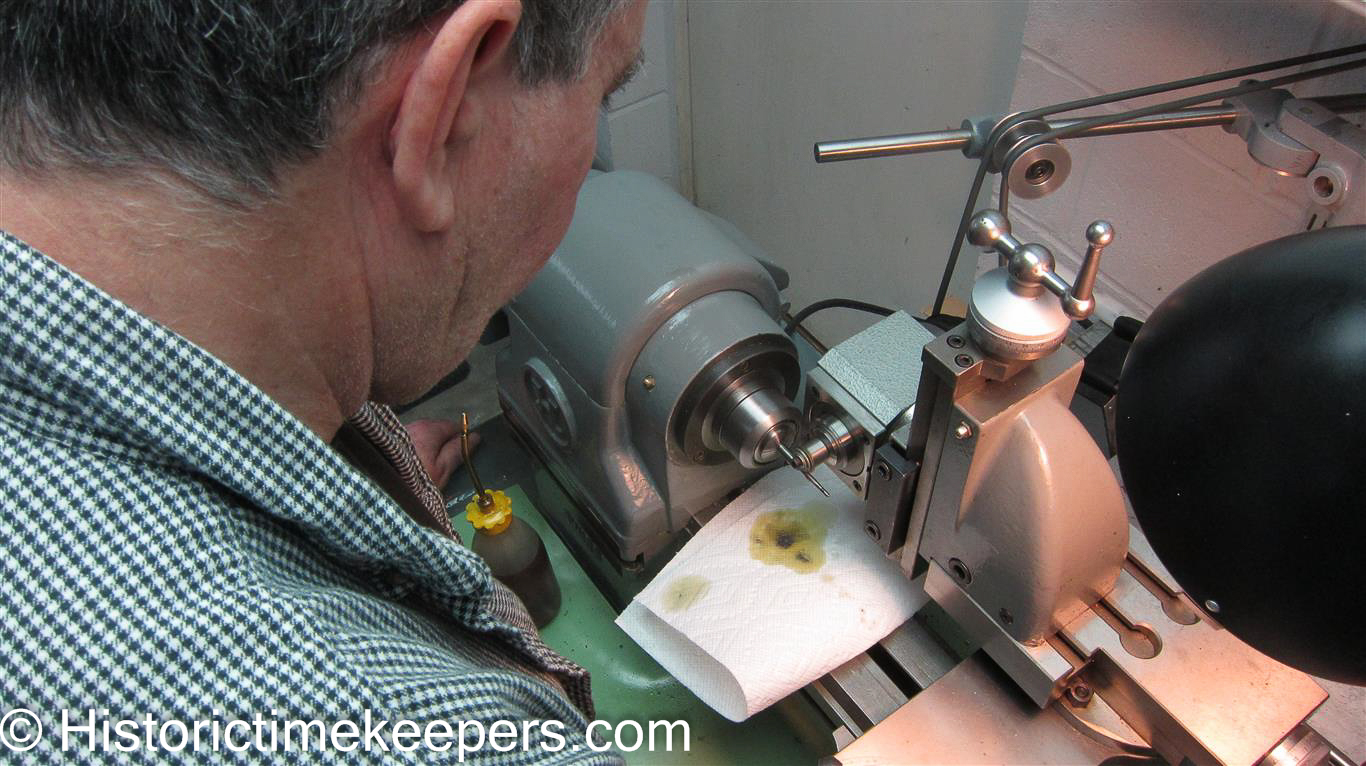 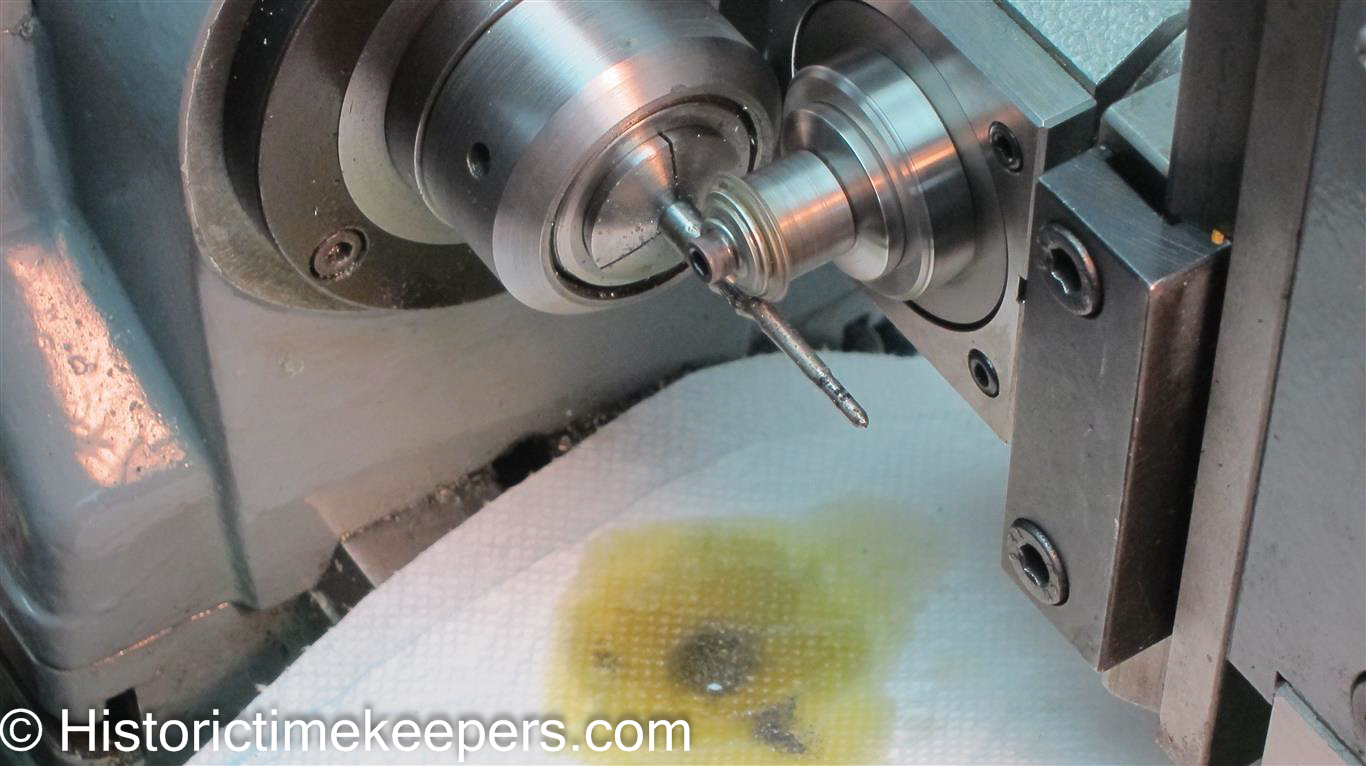 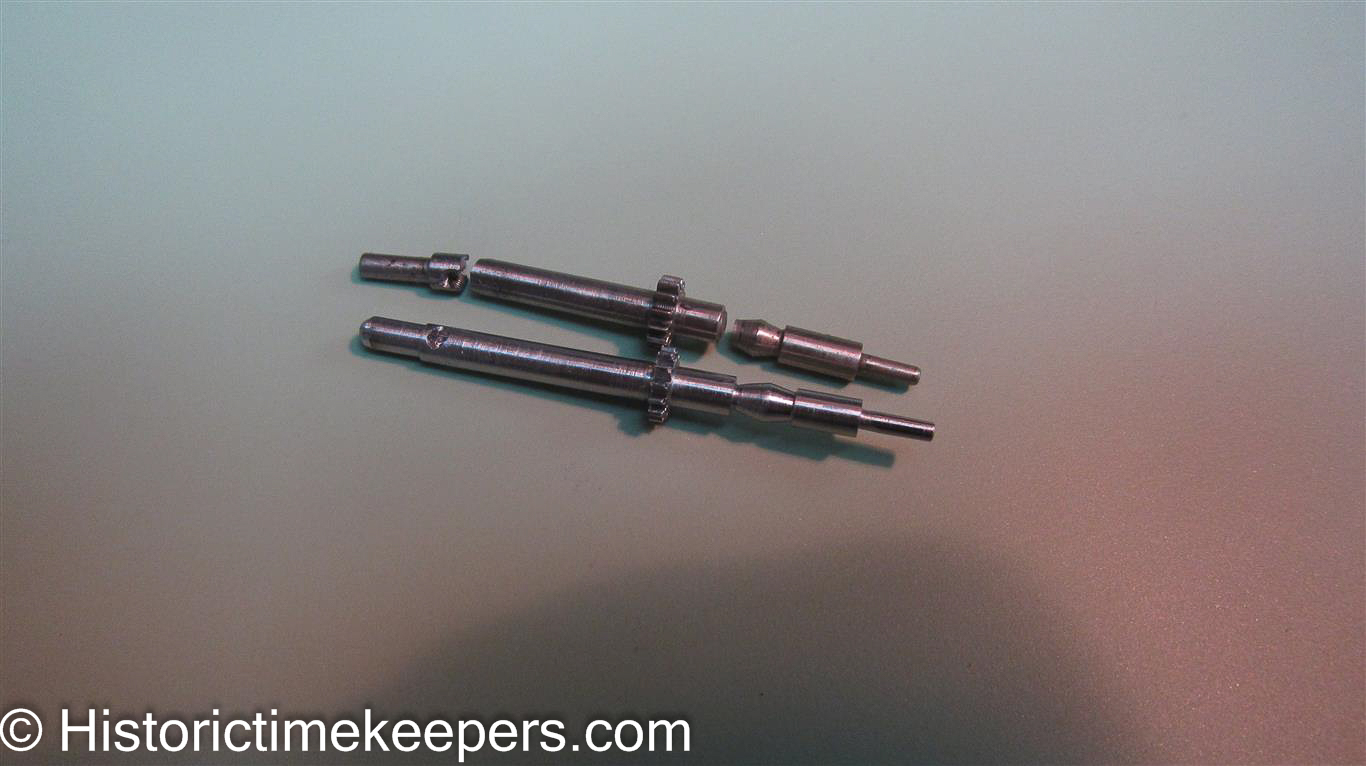
Finally comes the most important reason
for a watchmaker. Performance.
Everything previously mentioned is just
preparation. Reassembling an instrument and hearing it tick means
nothing to a watchmaker. He uses timing instruments to assess the
performance (beat, amplitude and rate deviations across positions) of the
piece. If it is not within spec, he knows how to make the
adjustments (no, this is NOT moving the fast/slow regulator) to bring it
within specifications. Especially for vintage pieces with steel
balance springs, it is vital that the movement be properly demagnetized if
precision timing is to be accomplished.
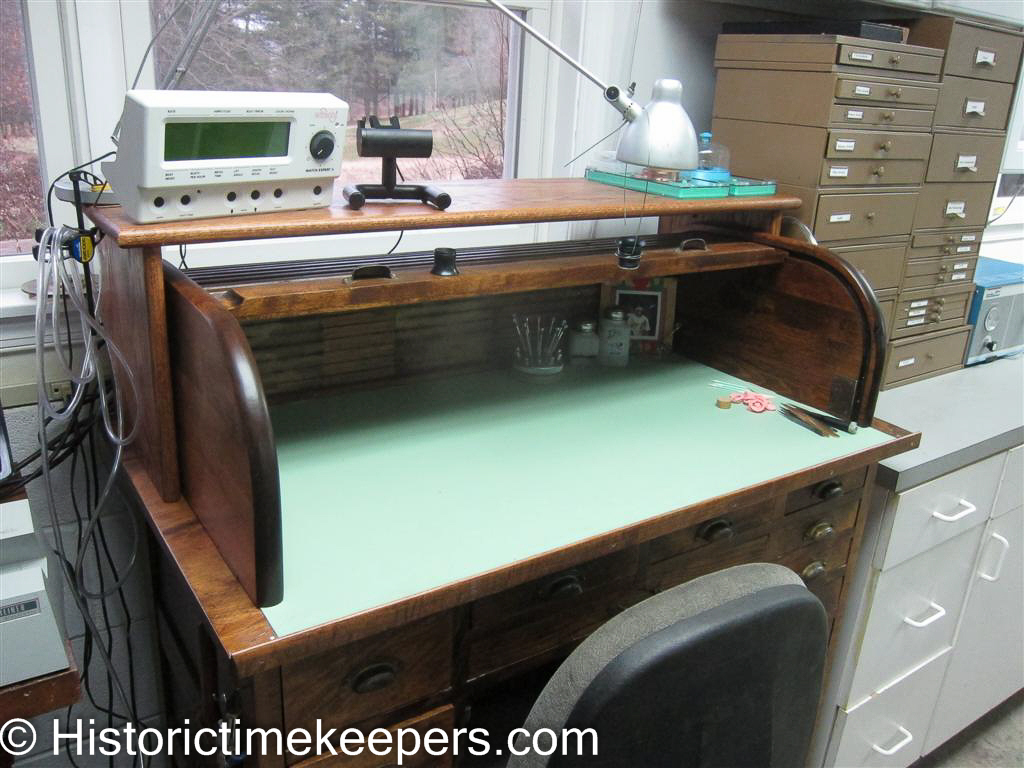
Clean work area and modern timing equipment

A modern demagnetizer is essential if precision timing
is expected from vintage teimpieces with steel balance springs
The timing instrument is a critical task
master and a disciplined watchmaker accepts it's judgment. Most of
the faults listed above would be immediately apparent during testing and a
watchmaker will go back and determine and apply the needed corrections.
HTI tests for a minimum of 7 days.
The equipment needed for this work is
expensive and may only be used 6 times a year (the escapement adjusting
tool is 500 CHF and if I use it 4 times a month that is a lot). A
specific pinion cutter may be used once every two years. But it is
all needed to be at hand.
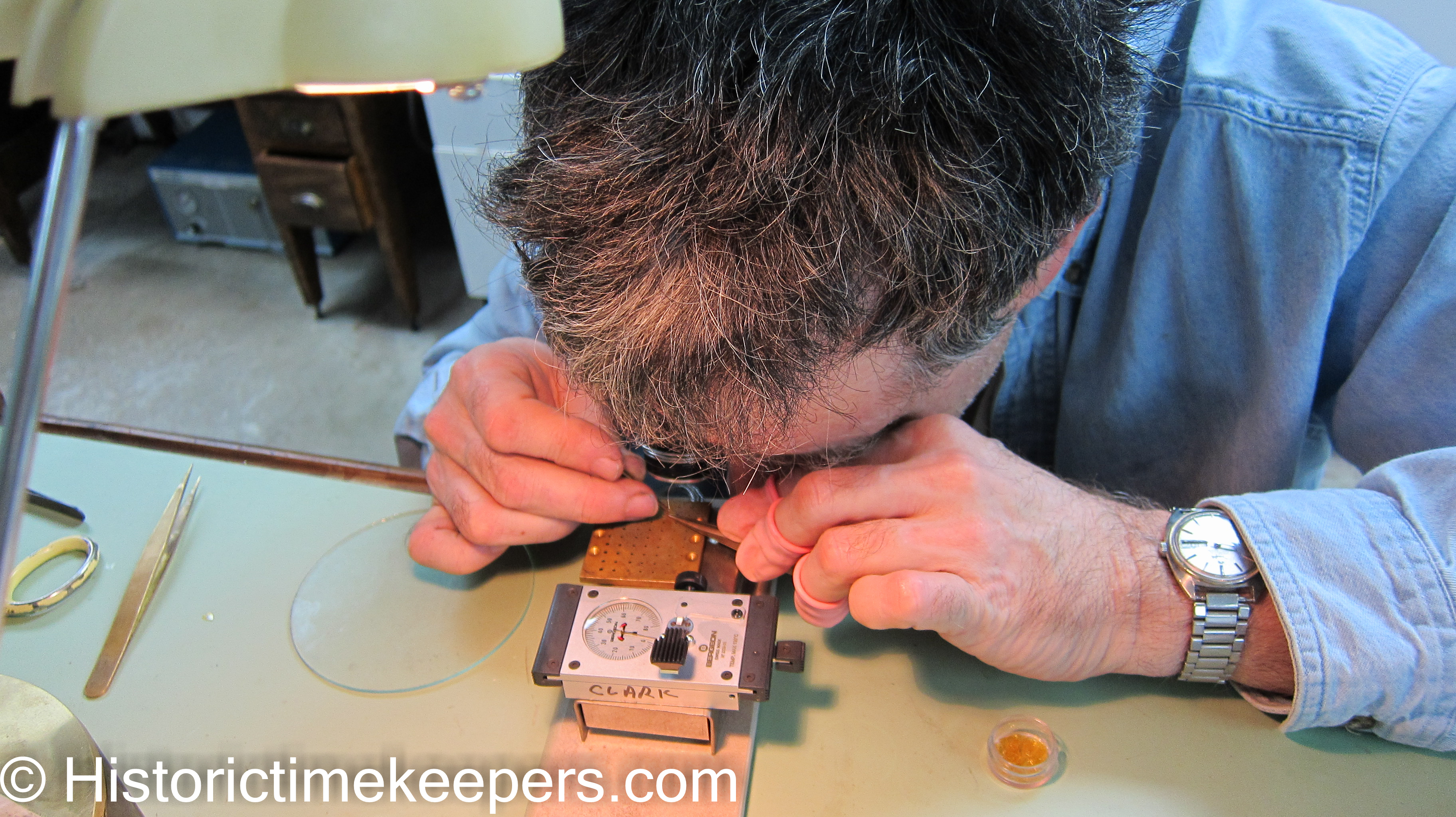
Using the escapement tool to make precise adjustments
to the pallet jewels in preparation for precision timing
But even more important is the training
in the theory and execution of precision timekeeping. It is not
something that can be self taught. I was fortunate enough to be
invited to Switzerland for a year of advanced training. Then there
is experience (in my case, 40 years) and judgment.
Here is an example of a very uncommon
instrument; a late 1930s RAF Swiss Time of Trip clock. The movt was
of a lower quality maker and not signed other than marked as of Swiss
manufacture. The issue was I could not uncase the piece because the
screw retaining the chrono pusher was rusted and the head stripped.
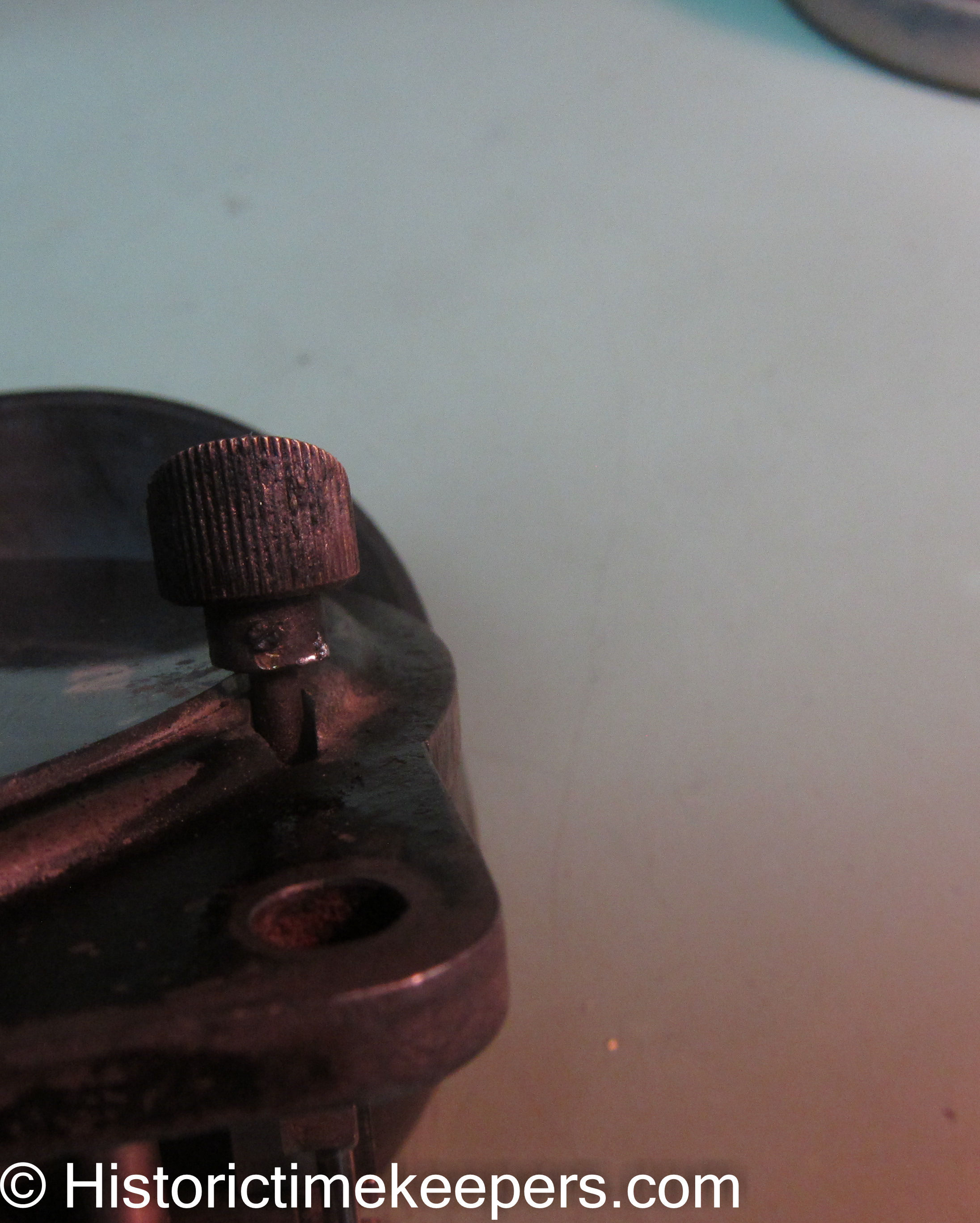
Screw rusted
and head deformed
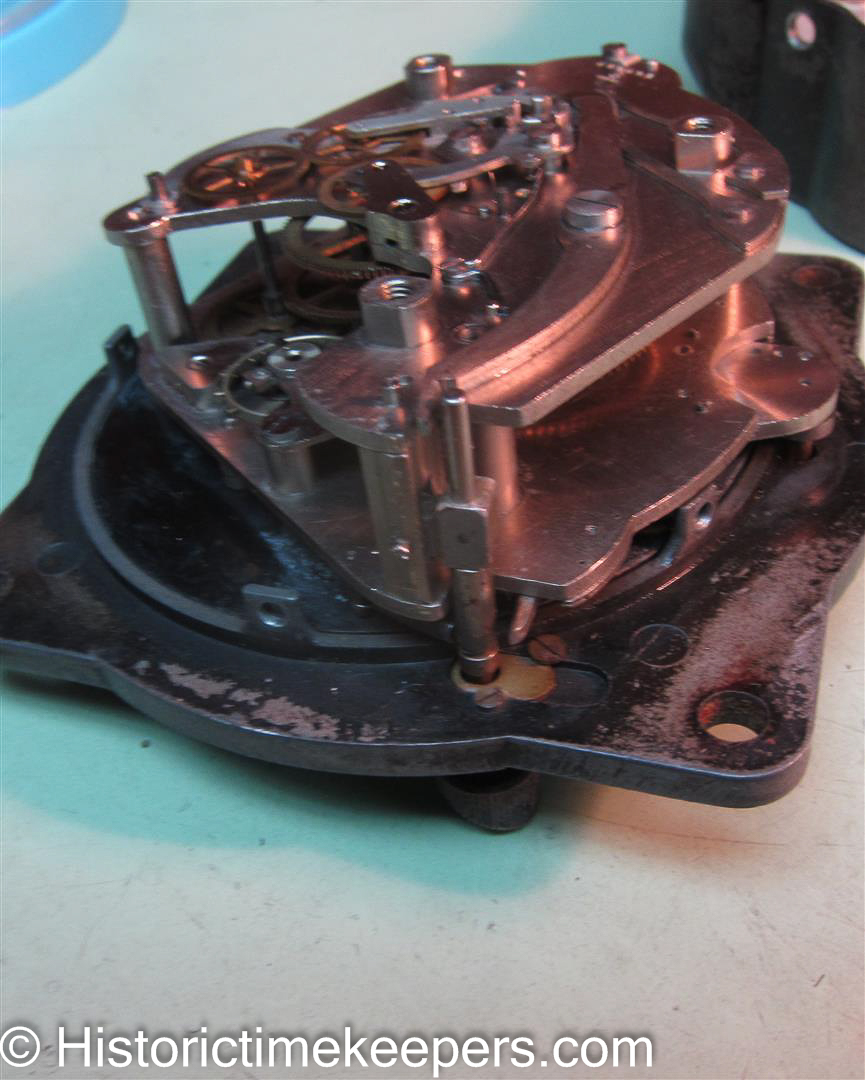
Arbor crosspinned to maintain knob orientation
There were two obvious considerations.
The knob and case must be preserved. There was no room to mount the
piece into the vise and mill the screw out. I COULD make the operating
arbor.
In consultation with the owner, I parted
the arbor just below the knob, allowing me to move on with the job.
I then dissolved what was left of the steel arbor and screw still in the
knob, leaving the knob as original. I then made the operating
arbor. The complete story of this piece can be found here.

Final result. Knob preserved, manufactured
arbor. Grub screw rather than cross pin.
The point is, micromachining is but only
one essential element of aircraft clock service and restoration. A
little sexier, but really akin to ensuring the surfaces are chemically
clean before applying lubricants. If you want your timepiece to
perform as intended, ask about the training of the worker. And at
Historic Timekeepers, Inc., you will receive a summary evaluation of your
instrument's performance that provides the same information used by Swiss
service centers to assess the quality of their work.
Finally, a word of caution: I do
not do work for other companies NOR do I sell my stainless steel
"unbreakable" mainsprings to others. Remember, precision
timing literally starts with a good mainspring. If I have to reuse
your old mainspring because there is nothing available I will tell you
BEFORE doing the work. If it prevents precision results, I
will discuss this with you before sending the final bill.
The biggest problem for the prospective
customer is to determine if the worker can actually get results. My
site serves two purposes, first to demonstrate to prospective customers
that I do the work cleanly and precisely without guesswork.
The other purpose is to provide some
guidance to those younger than me in their efforts to become skilled at
restoration work.
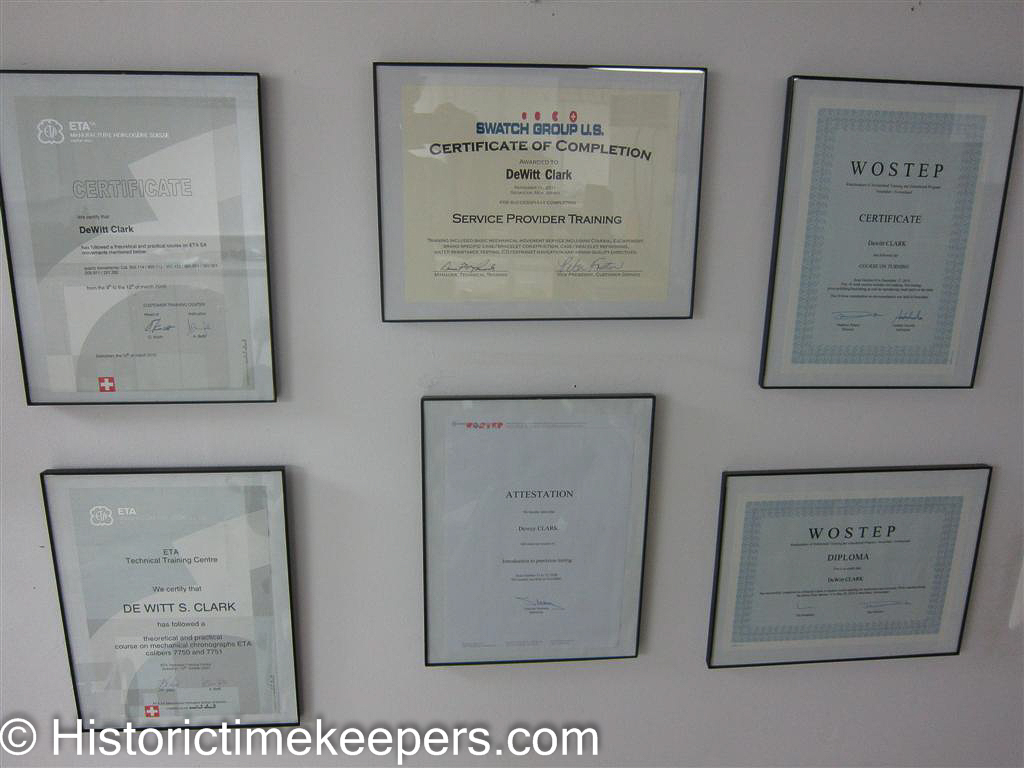
|