This clock is an example of the specialized work I perform and the
requests I satisfy. Unfortunately, damage (and the subsequent
cost) such as this can be avoided if the work is undertaken by a
qualified watch maker. It does not have to me; but the Approach to
Service page should give you some ideas of what to look for when
considering a workman. Do NOT rely on certifications; at best they
merely indicate that at one time the holder demonstrated the tested
skills. They say nothing about his/her motivation to do "good
work" outside the test process. Use your eyes and ears! To
restore the clock to function I had to first understand how it was
intended to operate. There are no service manuals (the Director of
Service for Omega USA told me this piece was always sent back to
Switzerland for service) and there is no information on the
internet. Even an "expert" I contacted refused to
respond to my request for photos. The
action of the jump seconds function is explained on a video
I uploaded to You Tube. Restoring the
jump seconds function required the manufacture of a 2mm OD 15 tooth
wheel and an index spring to fit on the index wheel. Here are some
photos of the finished wheel which is not much larger than the
"E" in in Liberty on a US dime. You can see it is
smaller than FDR's ear! 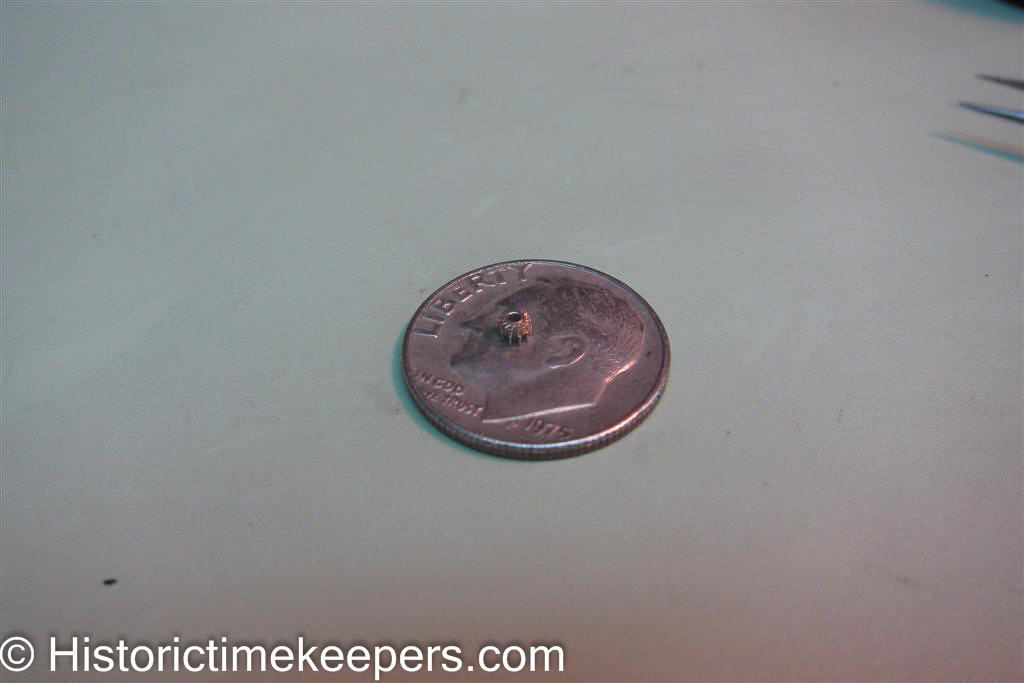
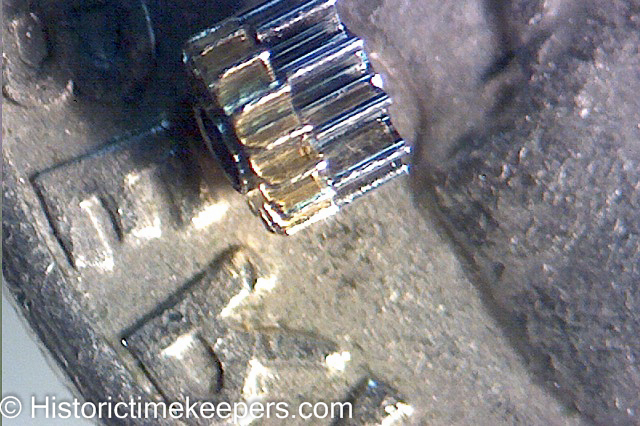 I
want to thank Blake Scott of Scotch
Watch. Upon finding this page he immediately sent me all the
information he had about this clock. This is the kind of
collegiality required in watchmaking today. The
pinion was made using my Habegger 102 Swiss lathe. More details
and examples about wheel and pinion cutting can be found in the Photoseries
section. 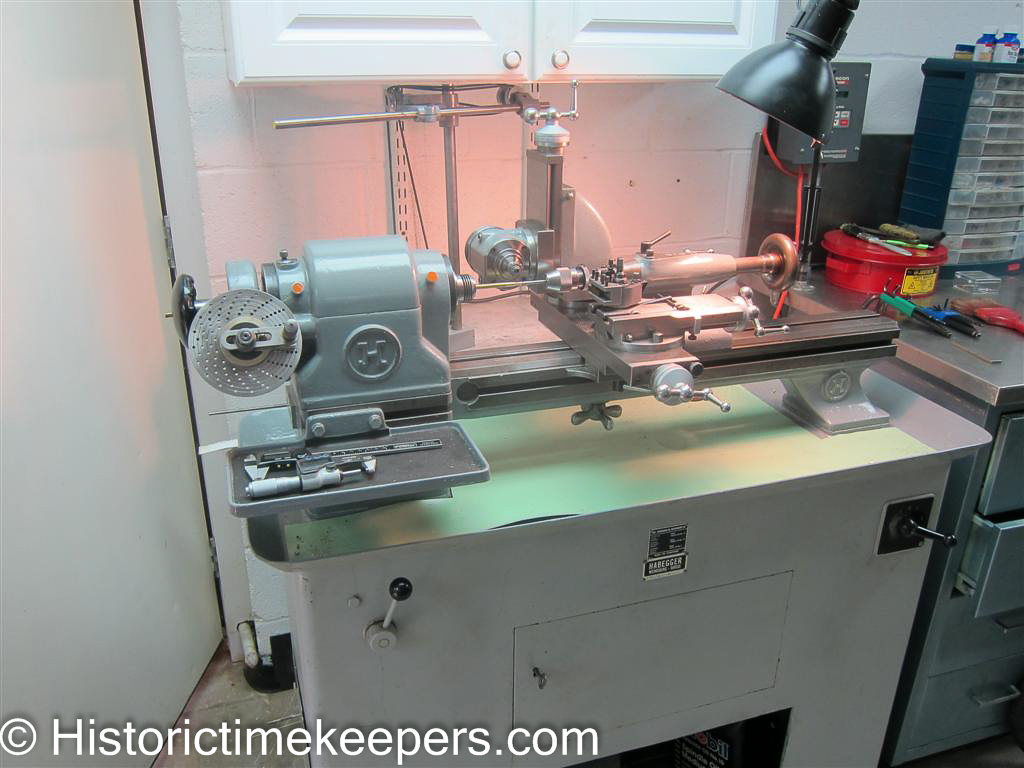
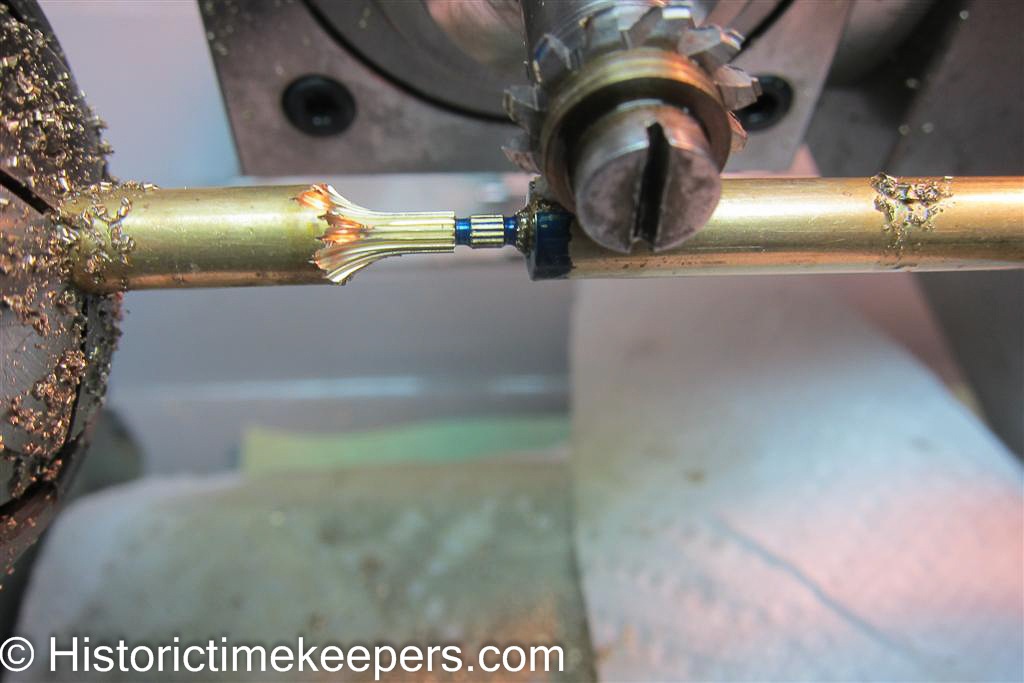
The customer agreed the importance
of the piece outweighed the cost of restoration. The spring
(broken by the previous workman) was made easily enough and had the
previous workman stopped there the additional charges would have been
minimal. But, as inexperienced watchmakers tend to do (and I
myself fell to this when I was learning), he made matters worse by
trying to "get out" of his error.
|